In the competitive landscape of chemical manufacturing in Egypt, operational efficiency plays a critical role in maintaining profitability and sustainability. Alnasr Chemicals Salt Factory, located in Giza, Egypt, faced challenges related to outdated processes, energy consumption, and productivity bottlenecks. To address these issues, the factory partnered with ENTRA, a leading provider of industrial optimization solutions, aiming to revolutionize its operations and achieve higher efficiency levels. This case study explores the strategies implemented by ENTRA and the transformative results that followed.
🚀 Project Summary
Client: Alnasr Chemicals Salt Factory
Industry: Chemical and Salt Manufacturing
Solution: Custom-designed Mega Belt Conveyor System
Objective: Increase material flow efficiency, reduce dust contamination, and minimize equipment downtime
🌍 Background
Alnasr Chemicals is one of the leading salt processing factories in Egypt, supplying a wide range of chemicals and salts for industrial use across the Middle East and North Africa (MENA). Like many factories in the region, Alnast faced increasing production demands while struggling with:
-
Material spillage due to manual handling and old conveyor systems
-
Frequent breakdowns caused by corrosion from salt exposure
-
Inconsistent flow rates across different processing zones
-
Dust generation affecting product quality and worker safety
They needed a robust, automated material handling system that could operate in a corrosive and dusty environment, handle bulk granular materials, and improve throughput without requiring frequent maintenance.
🔧 ENTRA’s Solution
After a site inspection and performance audit, ENTRA Electromechanical proposed a custom Mega Belt Conveyor system tailored for the salt manufacturing process.
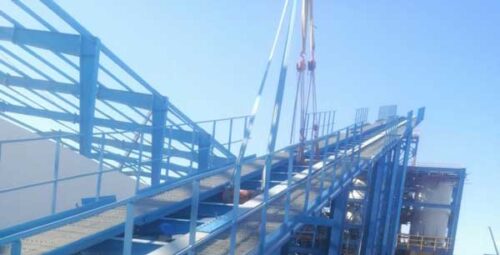
industrial conveyor structure
✅ Key Features of the Installed System:
-
Heavy Duty Steel construction for corrosion resistance
-
Dust-tight enclosures to prevent product loss and maintain air quality
-
Variable speed drive (VSD) to control flow rates in real time
-
Inclined Belt layout to save floor space
-
coated internal surfaces to minimize salt buildup
-
IP65-rated motor housing for wash-down and chemical resistance
🧠 Why ENTRA Was the Right Choice
ENTRA’s deep understanding of corrosive materials, experience in automating bulk handling systems, and local manufacturing capability made us the perfect partner for Alnast Chemicals.
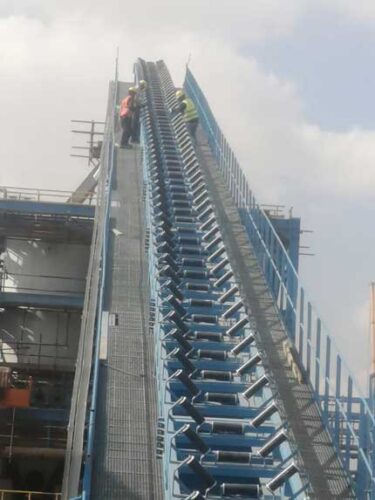
conveyor structre with roller guide
Enträ’s intervention was tailored to meet the specific needs of the salt manufacturing process. The core components of ENTRA’s solution included:
1. Digital Transformation and Automation
Enträ implemented automation systems to monitor, control, and optimize the production process in real-time. This involved deploying IoT sensors across key points such as evaporation ponds, crystallization units, and processing lines to gather data continuously.
2. Energy Optimization
Enträ’s advanced energy management tools were integrated to analyze consumption patterns and identify areas to reduce electricity and fuel usage, especially during peak demand periods.
3. Predictive Maintenance
By utilizing predictive analytics, ENTRA enabled Alnasr to anticipate equipment failures before they occurred, minimizing downtime and reducing maintenance costs.
4. Process Optimization
The solutions included process modeling and control strategies to improve crystallization efficiency and minimize waste, ensuring a consistent quality of salt.
5. Staff Training and Change Management
Enträ conducted comprehensive training sessions for Alnasr’s staff to ensure smooth adoption of the new systems and foster a culture of continuous improvement.
Implementation Phases
The project was executed in phased steps over six months:
- Phase 1: Assessment and Planning
- Detailed site analysis
- Identification of optimization opportunities
- Custom development of tailored solutions
- Phase 2: Deployment of IoT Sensors & Automation
- Installation of monitoring devices
- Integration with existing control systems
- Phase 3: Data Analysis & Optimization
- Calibration of control algorithms
- Staff training on new systems
- Phase 4: Monitoring & Fine-tuning
- Continuous performance monitoring
- Adjustments based on real-time data
Results and Benefits
The partnership between ENTRA and Alnasr resulted in remarkable efficiency gains and cost savings:
1. Increased Production Efficiency
Operational throughput increased by 20%, allowing Alnasr to produce more salt without expanding its physical footprint or energy consumption.
2. Energy Cost Reduction
Energy management strategies led to a 15% decrease in electricity and fuel costs, significantly impacting the factory’s bottom line.
3. Reduced Downtime
Predictive maintenance reduced equipment downtime by 30%, leading to more consistent product quality and increased overall equipment effectiveness (OEE).
4. Quality Improvement
Automation and tighter process controls resulted in a 10% improvement in salt purity and consistency, meeting international standards more reliably.
5. Enhanced Resource Utilization
Water and raw material consumption efficiencies lowered waste and reduced operational costs.
6. Environmental Impact
Energy savings and process improvements contributed to lower carbon emissions, supporting Alnasr’s sustainability goals.
7. Staff Empowerment
Training programs improved the skill set of employees and fostered a proactive approach to operational challenges.
Conclusion
The collaboration between ENTRA and Alnasr Chemicals Salt Factory exemplifies how modern digital solutions can revolutionize traditional industries. Through automation, real-time monitoring, and predictive analytics, ENTRA transformed Alnasr into a more efficient, cost-effective, and sustainable operation. This successful case underscores the importance of embracing Industry 4.0 technologies for manufacturing enterprises seeking to stay competitive in a rapidly evolving market.
Future Outlook
Building on this success, Alnasr plans to expand its use of digital tools further, exploring AI-driven quality control and advanced sustainability initiatives. ENTRA remains a strategic partner in this journey, continuously supporting their technological advancements.